3 Advances in water-based ink technology
By 1970, the main purpose of water-based inks was the corrugated paperboard industrial Kraft board offset printing line, which has gradually replaced moisture-cured alcohol-soluble letterpress printing inks.
They are colored half ester alkyl alkanolamine solutions of rosin maleic acid or fumaric acid. A major advancement in the 1970s that has implications for future development is the development of alkali soluble acrylic copolymers that cure faster and increase ink Dry and wet rub resistance on paper and wood substrates. Intermediate colloids and emulsion polymers have been further developed to improve the film formation of polymer solutions.
The development trend of material technology is shown in Figure 3, and Figure 4 shows the drying mechanism. Table 1 compares the performance of solvent-based and water-based inks, showing that the aqueous system has both its advantages and disadvantages. By the 1980s, color chips and paste concentrates that were easily dispersed in a suitable aqueous medium were developed.
Surfactants can improve pigment dispersion and printing properties.
The use of aqueous systems has limited progress in the following two aspects.
(1) In terms of the dryness of the ink, it takes more energy to volatilize water than volatilization of a similar boiling organic solvent.
(2) The impermeability of aqueous inks for packaging substrates is generally inferior to the corresponding organic solvent-based products in terms of adhesion, mechanical abrasion resistance, heat resistance, water resistance, and durability.
In the 1980s, the development enthusiasm for adopting a water-based system on a wider range of substrates was less than that in the United States and Europe, and the United States Environmental Protection Agency (EPA) began to impose limits on organic solvent emissions. In the United States, statistics show that water-based ink sales increase, and more and more began to use water-based offset printing and gravure printing inks for printing polyethylene, polyethylene sheathing and some film materials.
In the UK, early development of low-scent water-based gravure inks was used in chocolate and dessert packaging printing, as well as water-borne gravure varnishes on alcohol-soluble inks on food and preserve packaging materials. In fact, the market and application of these types of water-based varnishes are increasing year by year, not only in the field of offset printing and gravure printing, but also in the application of assembly line coatings (see Figure 2).
Corrugated box printing Kraft board printing has been used in a large number of water-based offset printing inks, and it is now also included that the white substrate before corrugating is printed with a high-quality four-color halftone (precoat white). There is no doubt that the more water-based inks are used, the more and more defects appear. Researchers need to continue research to improve and expand the range of water-based polymers available to improve their dry and print performance on plastics and other impermeable substrates. It is still a challenge to mainly consider the activity, such as achieving the balance of activity of the cross-linked polymer system and the required stability at high-speed printing.
By using synthetic resins, film-forming polymers and organic solvents more widely in liquid ink formulations, it has been possible to meet the printing needs of a wider range of substrates and laminate structures, and the range of aqueous systems is narrower. The polymer material used is more limited.
Then, with the legislation to control VOC emissions, how should we choose? Regarding the disputes on the route, the solvent recovery system has long been used in the gravure printing field of publications, but this is not feasible in the field of packaging and printing. In this case, a large number of different solvents need to be recovered and fractionated before use. Some articles discussed various controversial points in detail, discussed the advantages and disadvantages of various technologies, and discussed the impact of various factors including capital and operating costs. Solvents can be processed either biologically or thermally. Catalysts can be added or not. The biodegradation system utilizes a dispersion medium to adsorb VOCs in a moist environment and then uses specific bacteria that use it as a food source to decompose VOCs. The advantages are low operating costs, moderate capital costs, and long bacterial life. On the other hand, mutations in the concentration, composition, or flow rate of VOCs may stop bacterial work. This technique is suitable for low-concentration VOCs. The use of thermal oxidation incineration technology has the advantages of high-concentration VOC degradation, high efficiency, moderate capital cost, and compatibility with the fluidity, concentration, and composition of the released solvent.
With regard to flexible packaging printers and converters, thermal incineration equipment has been installed, and it is therefore unlikely that the newly developed water-based ink will be used.
It is expected that the interest in water-based inks for printing inks for paper and cardboard substrates will increase. In fact, some types of plastic films and films have already been used. Future research should focus on ways to improve the print dryness.
There are many factors that affect the final ink's dryness and quality. What is important is the air flow rate and optimum temperature for different ink and substrate mixing systems. How does the relative humidity affect the water evaporation rate?
Knowledge of the “dry curve†(see Figure 5) helps to understand what happens during the various volatilization phases. The development of accelerated drying techniques such as microwave and radio frequency radiation curing has become a priority.
4 Development trend and application of heat-cured screen offset lithographic printing ink
This brief description of changes in the formulation of thermosetting screen-printing inks that occurred in recent years was carried out in the 1970s. Detailed studies were conducted to save printing energy by making the formulated ink dry at the lowest possible oven temperature. There is no specific legislation on solvent emissions. However, the new ink uses a low-odor, high-boiling petroleum solvent and incorporates a small amount of water in the ink to form a water-in-oil emulsion without affecting lithographic performance. This allows lower-than-usual oven temperatures to be used. Despite these advances, some local authorities have insisted on solving solvent problems by discharging smoke from the stacks of drying ovens. In fact, incineration equipment has been installed, especially in areas with large buildings. factory.
This allows ink manufacturers to have a wider choice of inks such as high-boiling petroleum distillate (HBPF) solvents, using a new generation of polymer resins developed in recent years.
We have several different types and styles of Zipper bags to ensure that you can find the bags you need.
Crystal Clear Zipper Bags Bags of the highest clarity, our unique Polypropylene Crystal Clear zipper bags are great for displaying the true color of the contents while protecting them. These are the clearest zip bags in the industry.
PE Zippers Polyethylene Zipper bags that are flexible and with good resistance. Great for holding a variety of items.
White Block Zips Zip Bags made with a white block for easy labeling. Great for hardware stores, manufacturing companies, gift bags, and much more.Stand Up Zipper Pouches Bags most commonly used to package food that zip closed and make excellent display pieces.
Sliding Zips One of the most classic types of zipper bags, our wholesale sliding zipper bags are high clarity and cost well below retail pricing.
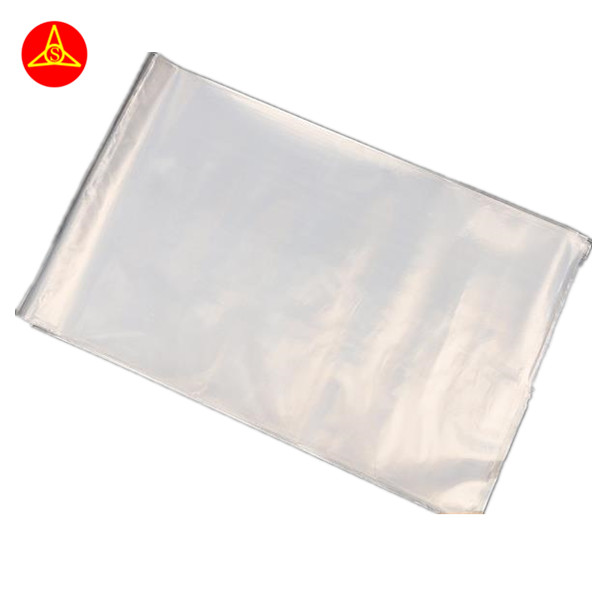
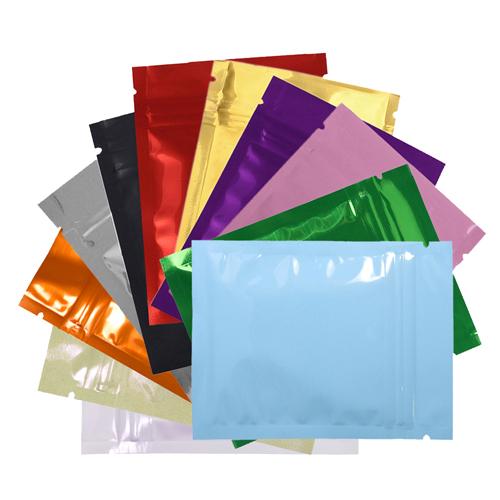
Zip Lock Plastic Bags,Zipper Lock Soybean Bag,Craft Plastic Bag,Brown Plastic Bag
DongGuan SanQun Packing Products Co.,Ltd , http://www.sanqunpacking.com