When conductive ink is printed, the ink will penetrate into the capillary holes, resulting in uneven impedance distribution of the electronic tag antenna. This phenomenon becomes more serious at higher frequencies. The adhesion of printed antennas, chip packaging and ink characteristics are important factors in determining the life of such products.
Foreword
With the growth of the RFID market, the use of electronic tags has also grown exponentially. But what really hinders the development of the RFID industry is that the price cost of electronic tags is still high, and printed electronic tags rely on innate cost advantages and are highly expected by the market.
Printed electronic technology is widely used in the fields of soft electronics, organic displays, EMI prevention, paper batteries, and RFID. Among them, RFlD passive electronic label printing faces the most technical difficulties.
Printing process
The main ink used in RFlD passive electronic label printing is commonly known as "conductive silver glue". Due to the need to use silver powder for printing, the recent rising price of raw materials has made the cost of silver glue high, resulting in the cost of printed electronic tags that originally had the advantage of manufacturing costs. The electronic label is still one of the best solutions for low-cost electronic labels in the future.
In the printing process, there are four major types of printing transfer inks: screen printing, gravure printing, letterpress printing, and inkjet printing. The characteristics, quality, and cost of each printing process are also different. Considering the characteristics of the printed substrate, the process of electronic label printing and the combination of material characteristics will determine the various electronic label printing places. Suitable production methods.
Screen printing
The printing process of the RFJD electronic label has the most cases of using this scheme. Screen printing is to sweep the conductive ink from the other side of the screen with a scraper to sweep the ink through the screen, and the ink penetrates the screen on the screen. The gap between holes is sticky printed on the printed substrate. The ink viscosity of screen printing is high, and the printing film thickness can be up to 100um, and the printing film thickness of RFID electronic tags is only about 8-12um, and then drying can be achieved by UV, IR, and hot air.
Gravure printing
Gravure printing is to fix a patterned metal thin plate (gravure) on a printing reel on a printing machine, transfer printing ink to the printed substrate. The ink viscosity of gravure printing is lower than the viscosity of screen printing ink. The ink film thickness control is the most accurate. It can also meet the film thickness requirements of RFlD electronic label printing, and the printing speed is faster. It is very suitable for mass printing production. It is a relatively high equipment investment.
[next]
Toppan Printing
In relief printing, a thick rubber plate (embossed) with a pattern is fixed on a printing reel on a printing machine, and transferred to the substrate after being dipped in printing ink. The ink viscosity of letterpress printing is lower than that of gravure printing, and the ink film thickness is much lower than the former two. The difficulties encountered when printing conductive silver paste are the highest and the most difficult to overcome, but if they can overcome all kinds of problems. The price competitiveness of printing electronic labels directly on cartons is unmatched by the first two.
Inkjet printing
The development of inkjet printing technology is an emerging technology in the past ten years. The printing accuracy of its large-scale inkjet printing equipment can be up to about 50um. This technology is also the most likely to successfully implement the IC circuit directly by printing in the process, but the disadvantages are The printing speed is slow. The cost of equipment and ink is also the highest among all printing processes, while the viscosity of ink is the lowest among the four processes, and the accuracy of film thickness control is the highest.
Conductive silver glue ink characteristics
At present, the suppliers of conductive silver adhesives are mainly American and European manufacturers. In Asia, there are Japanese and South Korean manufacturers competing. Their ink characteristics are mainly silver powder components, and the amount of silver powder components determines their conductive impedance characteristics.
Substrate
In the electronic label printing process, the most easily overlooked part is the substrate of the electronic label (substraie). In general, the types of substrates for passive electronic labels are nothing more than PVC, PET, coated white paper, satin paper, etc. However, if it is used in the UHF band, the dielectric coefficient of the substrate material will greatly affect the RF impedance of the electronic tag, so this factor must be considered when designing the electronic tag antenna.
When the electronic material label is printed on the substrate when using tiled paper, the capillary holes of the tiled paper are quite large and irregularly distributed. When conductive ink is printed, the ink will penetrate into the capillary holes, resulting in uneven impedance distribution of the electronic tag antenna. This phenomenon becomes more serious at higher frequencies.
Yield
The so-called yield rate here, in addition to whether the finished electronic tag can be read by the reader, the user is more concerned about the application yield rate, which is the so-called stable reading distance, and the key reason for this yield rate is the finished product RF impedance. In addition, the adhesion of printed antennas, chip packaging and ink characteristics are important factors that determine the life of such products.
[next]
Conductive impedance
The characteristics of the RF impedance of the printed electronic tag antenna will be determined by factors such as whether the solid content of the ink is evenly distributed in the ink during printing, the film thickness after printing, and the dielectric coefficient of the printed substrate. People in the world know that the color difference or film thickness of the first printed part to the last printed part will have a certain range of changes. If the quality factor of the substrate is added to produce a change in the dielectric coefficient, the result of the addition or cancellation of the two changes will cause the impedance of the electronic label printed antenna to exceed the specifications and produce defective products. The impact of the passive antenna printed on HF is relatively slight, but if this situation is encountered in the passive antenna printed on UHF, the probability of defective products will increase greatly. Even if the result of the addition or cancellation of the variation of the first two process variables does not make the electronic tag antenna printed impedance exceed the specifications, it will still produce different reading distance results for the printed UHF electronic tag.
Adhesion
When the substrate is smooth and compact, the ink may be easily peeled off after drying, especially when the semi-finished or finished product is curled, the dried film thickness will be peeled or cracked due to bending stress, but this situation The adhesion of the ink can be improved and improved by adjusting the resin in the ink.
Implant package
The yield of the implant process is mainly determined by the RF characteristics of the encapsulated conductive adhesive and the positioning accuracy of the printed parts. In general, the accuracy of the letterpress printing is the worst. If it can be planned in the process in the future, it will be considered when adjusting with the initial equipment construction. , Will effectively improve the yield of the implant process.
The life cycle
The life cycle of the printed electronic label is shorter than that of the electronic label made by etching, stamping or evaporation. The reason is that the silver paste after baking is in contact with water molecules or sulfur molecules in the air. It is easy to produce oxidation or vulcanization, and there is discoloration or blackening. If such printed electronic tags are used and affixed to goods that will be transported by sea, the oxidation or rumination phenomenon will be more severe. After the antenna is oxidized, creeped or vulcanized, the RF performance of the electronic tag will be affected by the depth of its changing layer, but fortunately, the thickness of the changing layer will not be obvious until the thickness of the changing layer reaches a certain depth. Variety.
in conclusion
When the above four printing methods are used for passive UHF electronic label printing, their costs and process yields are different. Although the yields of the two printing technologies of gravure and letterpress are low, the production cost and capacity of these two technologies But it is extremely competitive, and if there is a breakthrough in conductive ink materials in the future, the results in Figure (1) will be completely improved. Comparison of printing cost and yield. In addition, the cost of inkjet printing is still higher than that of gravure and letterpress printing technology. However, if the equipment investment cost is excluded, the price of conductive ink used in inkjet printing is the same as that of gravure and letterpress. The price of conductive ink is similar, and the process characteristics of low material loss and stable high yield make the overall production cost the lowest. Because the performance of the printed antenna mainly depends on the solid content of the conductive particles of the conductive ink, and the thickness of the printed film and other two process parameters, and these two parameters can control 74% of the process yield results, as shown in Figure (2) This shows that the yield of printed passive electronic label technology will be deeply affected by the characteristics of conductive ink materials.
Liquor is 90% marketing and what better way to grab attention than by having one of the coolest liquor bottles on the shelf? We should agree that taste is not the initial selling point for most consumers. That`s where marketing comes into play, and the bottle is a big part of that. An interesting look will get people to buy a brand at least once, and then it`s just a question of if the liquor inside is worth getting again. We would like to devote our passion on the Liquor`s dressing up.
Description
Usage
Liquor/Wine/Beverage
Material
Extra-flint, high-flint and flint glass
Technology
Machine made
Volume
50 to 3000ml or as your requirements
Weight
150 to 2000g and so on
Sealing type
Screw cap or cork
Painting
Any color as you requirement
Quality control
SGS, FDA, ISO9001, ISO14001
Deep processing
Silk screen, decal, spray painting,
electroplating, frosting, sand blasting.
Delivery term
EXW, FOB, CIF
Payment terms
T/T
Lead time
New design drawing confirm within 3days, Sample
mold within 20 days, bulk molds within 30 days, produce in bulk within 30 days
FAQ:
Q: Are you a manufacture or a trading company?
A: We are a manufacture which located in Chengdu city and Yibin city, Sichuan, China.
Q: Can you customize the products?
A: Yes, we are professional to customize glass bottle, we can design the new drawings and open the new molds according to your requirement.
Q: Do you provide free sample?
A: Yes, for cooperation sincerity, we are glad to provide you samples for free, but for new customer, the express cost need to be paid.
Q: What is your MOQ?
A: Our only standard for MOQ is a 40 feet container.
Q: How long is your sample lead time, mold need time and production lead time?
A: New design drawing confirm within 3 days, sample mold within 20 days, bulk molds within 30 days, produce in bulk within 30 days
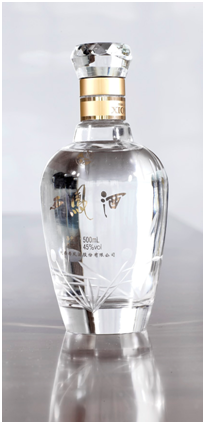
Wine Bottle
Wine Bottle,Round Wine Bottle,Decal Vodka Bottle,Red Character Wine Bottle
SICHUAN YIBIN GLOBAL GROUP CO.,LTD. , https://www.globalglassbottle.com